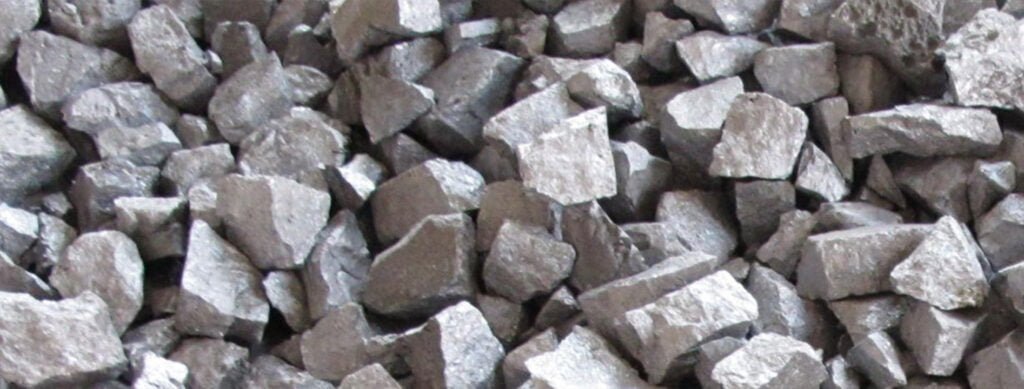
Ferro Silicon
Ferro-silicon (Fe-Si) is a metallic ferro-alloy having iron and silicon as its main elements. In commercial terminology, it is defined as a ferro-alloy containing 4 % or more of iron, more than 8 % but not more than 96 % of silicon, 3 % or less phosphorus, 30 % or less of manganese, less than 3 % of magnesium, and 10 % or less any other element. However, the regular grades of the ferroalloy normally contain silicon in the range of 15 % to 90 %. The normal silicon contents in the Fe-Si available in the market are 15 %, 45 %, 65 %, 75 %, and 90 %. The remainder is Fe and minor elements. The minor elements, such as aluminum, calcium, carbon, manganese, phosphorus, and sulphur are present in small percentages in Fe-Si. Fe-Si is normally used along with Fe-Mn as ladle addition during steelmaking.
Commercially, Fe-Si is differentiated by its grade and size. Fe-Si grades are defined by the percentages of silicon and minor elements contained in the product. The principal characteristic is the percentage of silicon contained in the ferro-alloy and the grades are referred to primarily by reference to that percentage. Hence 75 % Fe-Si contains around 75 % of silicon in it. Fe-Si grades are further defined by the percentages of minor elements present in the product. ‘Regular grade 75 % Fe-Si’ denote that the product containsw the indicated percentages of silicon and recognized maximum percentages of minor elements. Other grades of Fe-Si differ from regular grades by having more restrictive limits on the content of elements such as aluminum, titanium, and / or calcium in the ferro-alloy. Fe-Si is also produced in a grade which contains controlled amounts of minor elements for the purpose of adding them to steel or foundry iron using Fe-Si as the carrier. Such Fe-Si products are sometimes called ‘inoculants’.
Fe-Si is normally produced in four grades. These are (i) standard grade, (ii) low aluminum grade, (iii) low carbon grade, and (iv) high purity grade having low content of titanium. The standard grade of Fe- Si contains aluminum upto 2 % while the low aluminum grade has aluminum content of 0.5 % maximum. Fe-Si contains a high proportion of iron silicides. Fe-Si with 15 % silicon is not used for metallurgical purposes in the production of steel or cast iron. Specialty grade 15 % Fe-Si is combined with water to create a dense medium for gravity (sink / float) separation of minerals, aggregates, and metals.
Fe-Si is mainly used during steelmaking and in foundries for the production of carbon steels and stainless steels as a deoxidizing agent, for the alloying of steels, and cast iron. It is used as a reducing agent, particularly in the production of stainless steel. As a reducing agent, silicon reacts with chromium oxides to form silicon oxides, returning chromium to the liquid steel, and thus increasing the overall chromium recovery of the process.
Fe-Si is also used as the source of silicon for alloying purposes in the production of certain steel alloys, particularly silicon electrical steel, which can contain 3 % or more of silicon. Fe-Si is used by iron foundries as the source of silicon needed for alloying purposes in iron castings. During the production of cast iron, it is also used for inoculation of the iron to accelerate graphitization. In arc welding, Fe-Si can be found in some electrode coatings.
Almost all Fe-Si consumed in the steel and cast iron industry contains silicon ranging from 65 % to 90 %. Fe-Si is used primarily in sized lump form. Size is important since it affects the performance of the Fe-Si in its designated use. Large lumps are normally used in primary steelmaking furnaces since they penetrate the layer of slag on top of the liquid steel more readily. Smaller lumps are more commonly used for alloying purposes to ensure rapid dissolution in liquid steel. Fines are less desirable than lumps since it is more difficult to recover the silicon content in them.
Commercially, Fe-Si is differentiated by its grade and size. Fe-Si grades are defined by the percentages of silicon and minor elements contained in the product. The principal characteristic is the percentage of silicon contained in the ferro-alloy and the grades are referred to primarily by reference to that percentage. Hence 75 % Fe-Si contains around 75 % of silicon in it. Fe-Si grades are further defined by the percentages of minor elements present in the product. ‘Regular grade 75 % Fe-Si’ denote that the product containsw the indicated percentages of silicon and recognized maximum percentages of minor elements. Other grades of Fe-Si differ from regular grades by having more restrictive limits on the content of elements such as aluminum, titanium, and / or calcium in the ferro-alloy. Fe-Si is also produced in a grade which contains controlled amounts of minor elements for the purpose of adding them to steel or foundry iron using Fe-Si as the carrier. Such Fe-Si products are sometimes called ‘inoculants’.
Fe-Si is normally produced in four grades. These are (i) standard grade, (ii) low aluminum grade, (iii) low carbon grade, and (iv) high purity grade having low content of titanium. The standard grade of Fe- Si contains aluminum upto 2 % while the low aluminum grade has aluminum content of 0.5 % maximum. Fe-Si contains a high proportion of iron silicides. Fe-Si with 15 % silicon is not used for metallurgical purposes in the production of steel or cast iron. Specialty grade 15 % Fe-Si is combined with water to create a dense medium for gravity (sink / float) separation of minerals, aggregates, and metals.
Fe-Si is mainly used during steelmaking and in foundries for the production of carbon steels and stainless steels as a deoxidizing agent, for the alloying of steels, and cast iron. It is used as a reducing agent, particularly in the production of stainless steel. As a reducing agent, silicon reacts with chromium oxides to form silicon oxides, returning chromium to the liquid steel, and thus increasing the overall chromium recovery of the process.
Fe-Si is also used as the source of silicon for alloying purposes in the production of certain steel alloys, particularly silicon electrical steel, which can contain 3 % or more of silicon. Fe-Si is used by iron foundries as the source of silicon needed for alloying purposes in iron castings. During the production of cast iron, it is also used for inoculation of the iron to accelerate graphitization. In arc welding, Fe-Si can be found in some electrode coatings.
Almost all Fe-Si consumed in the steel and cast iron industry contains silicon ranging from 65 % to 90 %. Fe-Si is used primarily in sized lump form. Size is important since it affects the performance of the Fe-Si in its designated use. Large lumps are normally used in primary steelmaking furnaces since they penetrate the layer of slag on top of the liquid steel more readily. Smaller lumps are more commonly used for alloying purposes to ensure rapid dissolution in liquid steel. Fines are less desirable than lumps since it is more difficult to recover the silicon content in them.
Lump Size 10-60 MM 90% Minimum
- ELEMENTS
- Silicon %
- Aluminum %
- Phosphorus %
- Carbon %
- GRADE
- 70 Minimum
- 1.50 Maximum
- 0.05 Maximum
- 0.20 Maximum