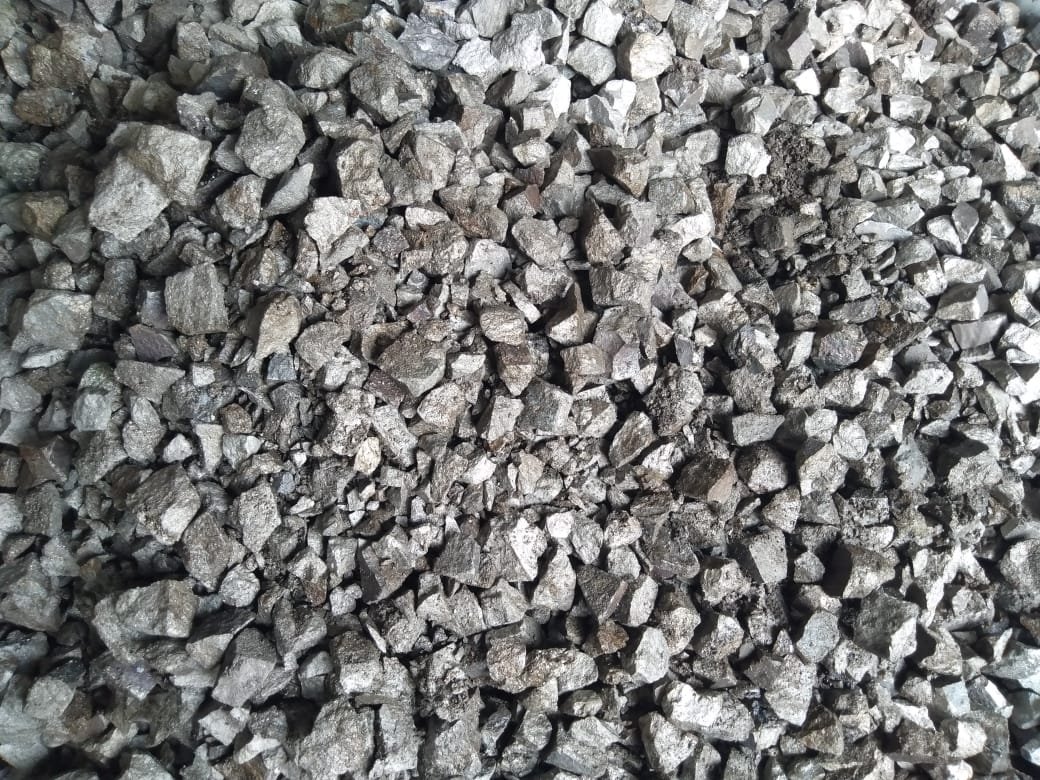
Silicon Manganese
Si-Mn is a ferroalloy consisting mainly of manganese, silicon and iron. It usually contains much smaller proportions of minor elements such as carbon, phosphorus and sulphur. The ferroalloy is sometimes also called ferro-silicon-manganese. It is used to add both silicon and manganese as a ladle additive in steelmaking. Si-Mn is produced in various grades and sizes and is used in bulk form primarily in steelmaking as a source of Si and Mn, although some Si-Mn is also used as an alloying agent in the production of iron castings. Because of its lower carbon content, it is a preferred ladle additive in the production of low carbon steels. Both manganese and silicon play an important role in the production of steel as deoxidisers, desulphurisers and alloying agents. Si-Mn adds additional silicon to liquid steel which is a stronger deoxidiser and also helps to improve some mechanical properties of the steel.
Si-Mn with a high content of manganese and silicon is produced by heating a mixture of manganese (MnO2) silicon (SiO2) and iron (Fe2O3) oxides with carbon in a furnace. These oxides undergo a thermal decomposition reaction. The standard grade contains 62% to 68% manganese, 12% to 18% silicon and about 2% carbon. The low-carbon Si- Mn grade has a maximum carbon content of 0.1%. Si-Mn is the ferroalloy preferred by steel mill operators for deoxidisation. The steel industry is the only buyer of these alloys.
To meet the demand for Mn and Si, the steelmaker has a choice between a mixture of Si-Mn, Fe-Mn with high carbon content and Fe-Si which is determined by the specifications for carbon, silicon and manganese. In the past, a mixture of high-carbon Fe-Mn and Fe-Si was usually used, but there is now a trend towards greater use of Si-Mn at the expense of the other two. This is mainly for economic reasons.
The effects of adding Si-Mn to steel depend on the amount added and the combined effect with other alloying elements. Both Si and Mn have an important influence on the properties of steel as they both have a strong affinity for oxygen and act as deoxidants. Deoxidation with Si-Mn results in cleaner steel because the liquid manganese silicate formed coagulates and separates from the melt, more easily than the solid SiO2 formed in Fe-Si deoxidation. The use of Si-Mn adds less carbon to the steel than the combination of standard Fe-Si and high carbon Fe-Mn. Calculations using computational fluid dynamics show that the yield of silicon from Si-Mn is higher than that of standard Fe-Si.
Si-Mn with a high content of manganese and silicon is produced by heating a mixture of manganese (MnO2) silicon (SiO2) and iron (Fe2O3) oxides with carbon in a furnace. These oxides undergo a thermal decomposition reaction. The standard grade contains 62% to 68% manganese, 12% to 18% silicon and about 2% carbon. The low-carbon Si- Mn grade has a maximum carbon content of 0.1%. Si-Mn is the ferroalloy preferred by steel mill operators for deoxidisation. The steel industry is the only buyer of these alloys.
To meet the demand for Mn and Si, the steelmaker has a choice between a mixture of Si-Mn, Fe-Mn with high carbon content and Fe-Si which is determined by the specifications for carbon, silicon and manganese. In the past, a mixture of high-carbon Fe-Mn and Fe-Si was usually used, but there is now a trend towards greater use of Si-Mn at the expense of the other two. This is mainly for economic reasons.
The effects of adding Si-Mn to steel depend on the amount added and the combined effect with other alloying elements. Both Si and Mn have an important influence on the properties of steel as they both have a strong affinity for oxygen and act as deoxidants. Deoxidation with Si-Mn results in cleaner steel because the liquid manganese silicate formed coagulates and separates from the melt, more easily than the solid SiO2 formed in Fe-Si deoxidation. The use of Si-Mn adds less carbon to the steel than the combination of standard Fe-Si and high carbon Fe-Mn. Calculations using computational fluid dynamics show that the yield of silicon from Si-Mn is higher than that of standard Fe-Si.
SILICON MANGANESE (LUMP SIZE 10-60 MM, 90% MIN)
- ELEMENTS%
- Mn%
- Silicon%
- Carbon%
- Sulphur%
- Phos%
- HIGH CARBONGRADE
- 65Min | 65Min
- 14 Min | 16 Min
- 2.5 Max | 2 Mix
- 0.03 Max | 0.03 max
- 0.30 Max | 0.30 Max
- MEDIUM CARBONGRADE
- 55-58 Min
- 22-25 Min
- 0.50 Max
- 0.05 Max
- 0.15-0.20 Max
- LOW CARBONGRADE
- 55-60 Min
- 25-30 Min
- 0.10 Max
- 0.03 Max
- 0.10 Max